Press Room
Hovione expands nasal drug delivery capabilities with the development of nasal powder delivery device technology in collaboration with IDC
Hovione, the specialist integrated CDMO, just announced an expansion of its nasal drug delivery capabilities with the addition of a family of innovative nasal powder delivery devices developed in partnership with IDC.
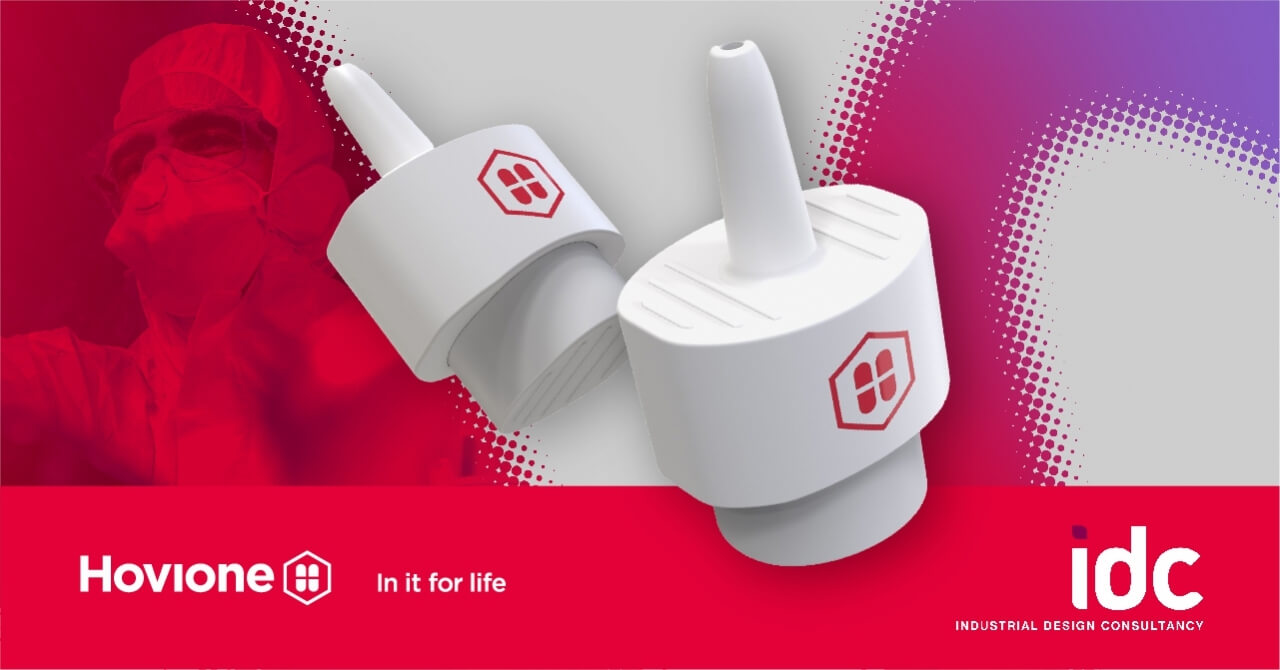
- Hovione and Industrial Design Consultancy (IDC) have entered into a joint development of an innovative nasal powder delivery device technology supporting local, systemic, and nose-to-brain drug delivery.
- Nasal delivery is a simple and safe alternative to conventional delivery routes for drug delivery, which offers a faster onset of action. It is also seen as a promising pathway to deliver new drugs to the brain and treat diseases of the central nervous system.
Lisbon, November 29, 2023, Hovione, the specialist integrated CDMO, leader in spray drying and particle engineering, just announced an expansion of its nasal drug delivery capabilities with the addition of a family of innovative nasal powder delivery devices developed in partnership with IDC. Intranasal drug delivery is a good alternative to conventional delivery routes for both local and systemic drug delivery due to its simplicity, safety, and faster onset of action. Additionally, it is emerging as a promising pathway to deliver new drugs to the brain to treat diseases of the central nervous system (CNS).
Hovione and IDC have been working together to accelerate the development and commercialization of two new active nasal powder delivery devices, one single-use and one multidose. The devices enable broad and targeted nasal deposition flexibility while delivering maximum usability and reliability. By using standard capsules and filling equipment, they also have the potential to simplify drug product development and manufacturing.
"Intranasal drug delivery is gaining momentum across a number of applications, including mucosal vaccination and CNS treatments bypassing the blood-brain barrier", says Dr. Jean-Luc Herbeaux, Hovione's CEO. He adds: "Our partnership with IDC, a company with vast experience in industrial design, mechanical and electronic engineering of medical devices, enables Hovione to offer a complete solution for nasal powder delivery – covering Active Pharma Ingredients (APIs), formulation, filling, analytics and device design and manufacturing - that address the needs of pharmaceutical companies and patients".
“By combining Hovione’s capabilities in pharmaceutical development, formulation and manufacturing with IDC’s device development expertise, this partnership offers customers a nasal powder delivery solution which can be rapidly adapted to new pharma compounds and therapies” explains IDC´s Managing Director, Dr Stephen Knowles, “Our joint development team has done incredible work to create unique, high performance nasal powder delivery devices.”
Hovione will offer the new devices on an exclusive basis as part of its integrated offer for nasal drug development and manufacturing.
About Hovione:
Hovione is an international company with over 60 years of experience in pharmaceutical development and manufacturing operations. As a Contract Development and Manufacturing Organization (CDMO) it has a fully integrated offering of services for drug substances, drug product intermediates and drug products. The company has four FDA-inspected sites in the USA, Portugal, Ireland and China and development laboratories in Lisbon, Portugal and New Jersey, USA. Hovione provides pharmaceutical customers services for the development and compliant manufacture of innovative drugs, including highly potent compounds, and customized product solutions across the entire drug life cycle. In the inhalation area, Hovione offers a complete range of services, from API, formulation development and devices.
Hovione's culture is based on innovation, quality and dependability. Hovione was the first Chemical/ Pharmaceutical Company to become a Certified B Corp, is a member of Rx-360, EFCG and participates actively in industry quality improvement initiatives to lead new global industry standards.
About IDC:
IDC is a leading medical product design and development consultancy dedicated to using its creativity, insight, experience and expertise to make the best possible products and deliver commercially successful products for clients and partners. With over 50 years’ experience and ISO13485 compliant processes and facilities in London and Shanghai, IDC’s experts in user research, design, mechanical and electronics engineering and rapid prototyping work to create award-winning, world-leading products for global markets.
IDC’s track record includes many commercialized drug delivery devices across inhalation, nasal and injectables with a focus not just on design but also ensuring a smooth transition to production and regulatory approvals. IDC’s mission statement is “We innovate to create successful products which improve people’s lives”.